APPLICATION CENTER FOR SURFACE TECHNOLOGY (AOT)
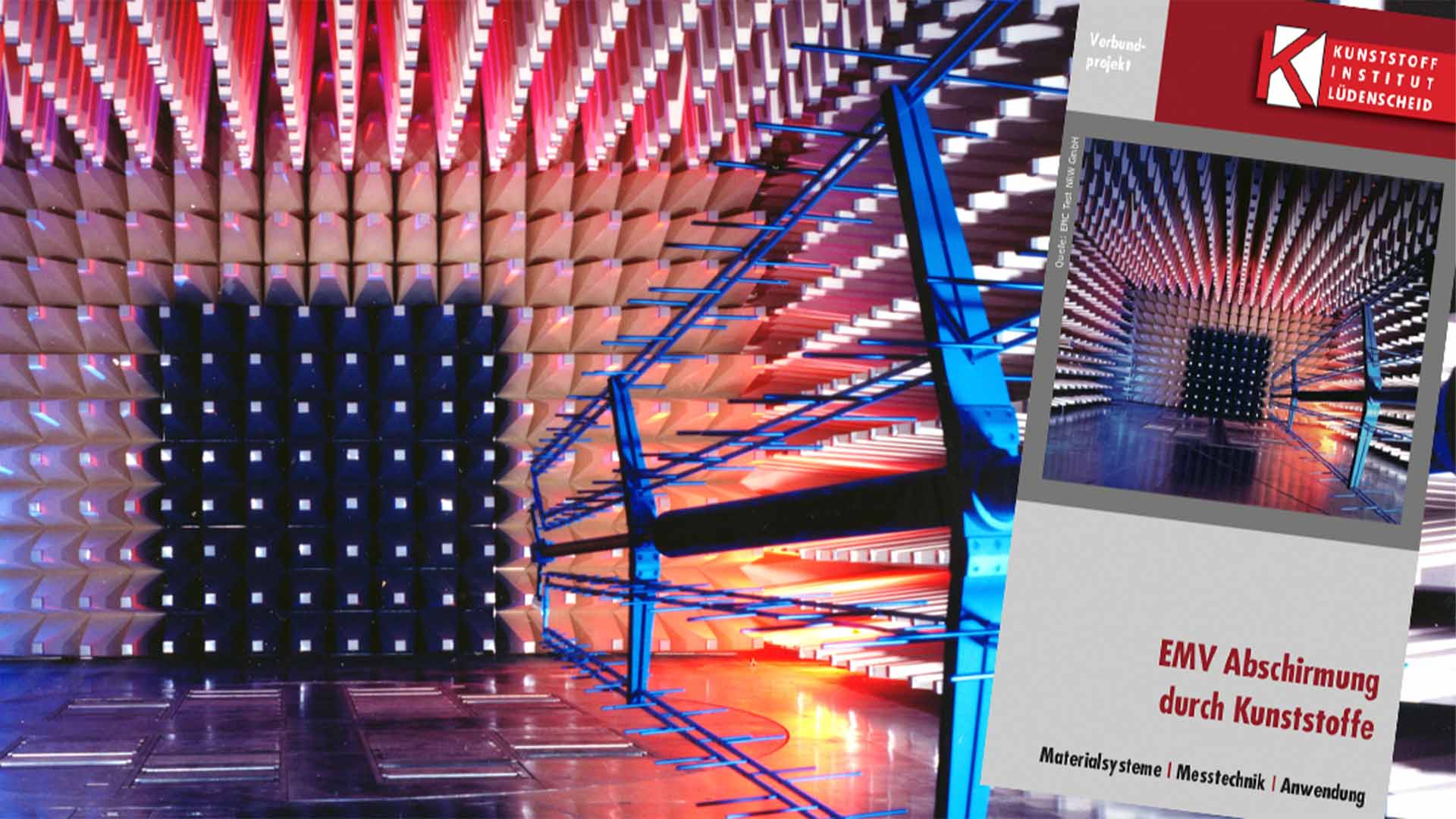
Due to new design concepts and simultaneous technical function integration, cases of electronic components require innovative solutions with regard to the material. Electrically conductive plastics can contribute to the trouble-free operation of electronic systems, particularly with regard to shielding against electromagnetic radiation. Technology drivers are advancing digitalization, electrification and the increase in radio applications in the automotive, electronics, household or medical sectors. Devices must function or interact side by side without unintentionally influencing each other.
On the one hand, the project dealt with material technology issues. Conductive plastics for EMC applications, based on fillers such as carbon, steel or conductive carbon black, are nowadays well established. The use of the fillers increases the stiffness of the material, but at the same time reduces important housing properties such as impact strength and elongation at break. The toughness and elongation of conductive plastics can be optimized by using modifiers. Currently unresolved is the effect on conductivity and shielding effectiveness, which are being investigated in this project.
On the other hand, the connections of case components (e.g. by screws) require special consideration with regard to the joining situation. In contrast to metallic materials, plastics exhibit increased contact resistance in the joining area, which has a detrimental effect on the shielding behavior. By choosing more suitable geometry modifications, the penetration and leakage of electromagnetic waves can be prevented. The study of the influence of geometry variation was initially performed using 3D printing. This was followed by the injection molding of cases to evaluate the influence of different materials.